Если миф о не гниющем лужёном кузове “Победы” уже не пользуется былой популярностью, то возникший фактически в ответ на него контр-миф про то, что использование припоя – не более, чем следствие низкого качества штамповки, а использовался он для маскировки возникающих при ней многочисленных дефектов, увы, всё ещё жив и периодически “подёргивает ножкой”, время от времени попадая в ленты посвящённых отечественному автопрому сообществ.
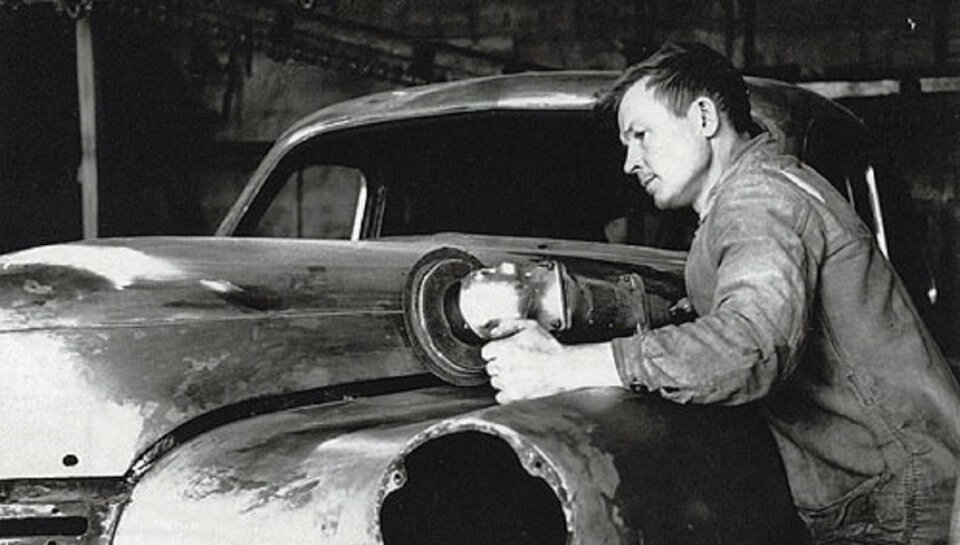
В частности – с чьей-то лёгкой руки по Интернету стала гулять информация о том, что на кузове этого автомобиля “олова”, использованного на заводе для исправления вмятин и прочих дефектов, якобы настолько много, что именно оно, а не сталь, преимущественно определяет форму его кузова, а общее его количество на каждом кузове «Победы» достигает «70 килограммов» (конкретная цифра может варьировать — 15, 17, 20, 25, 50 килограммов… кому сколько не жалко). Миф этот довольно-таки обидный и в целом не более близкий к реальности, чем легенда о “лужёном кузове”, но всё же имеющий под собой определённое историческое основание; какое именно – скоро увидим.
Реальность, в кратком изложении (а более подробно к этому вопросу мы ещё будем возвращаться, и не раз), выглядела примерно так: припой (состоящий в основном из свинца, с добавкой 20-30% олова) в те годы использовался на автозаводах по всему миру, причём главным образом не “вместо шпаклёвки”, а в тех местах, где шпаклёвка в принципе применена быть не может – при герметизации швов сварки и стыков кузовных панелей. То есть, как своего рода аналог современного шовного герметика. Правда, с одной существенной оговоркой: обработка швов кузова в сороковые – пятидесятые годы это совсем не то же самое, что их обмазывание шовным герметиком в наше время; требования к их внешнему виду были совсем другими, и во многих случаях швы почти буквально «штукатурились» припоем до полностью гладкой поверхности, так что толщина его слоя могла достигать нескольких миллиметров. Но это было как раз нормальной, предусмотренной конструкцией автомобиля технологической операцией, а не маскировкой дефектов.
Почему не получалось обойтись без такого трудоёмкого процесса ? Причины были многообразны, но главной из них было то, что кузова были спроектированы и изготовлены совсем не так, как это делается сегодня. В частности – вместо широко используемой сегодня сварки кузовных панелей “за отбортовки” использовалась сварка “внахлёст”, когда одна панель накладывалась на другую и прихватывалась к ней точками сварки. И таких швов было много, потому что в те годы вызывала проблемы крупногабаритная штамповка, требовавшая сложного и дорогостоящего производственного оборудования. Поэтому кузова, включая проёмы дверей, сваривались “из кусочков”, с большим количеством швов между ними – в том числе довольно грубых, выполненных газовой или ручной дуговой сваркой сплошным швом, что приводило к деформации панелей и необходимости ручной рихтовки и заполнения шва припоем. Это было характерно далеко не только для отечественных автомобилей, но и (в различной степени) для всех выпускавшихся в тридцатые, сороковые и начале пятидесятых годов, причём в особенности увеличилось количество швов после перехода на имевшие более сложную форму “понтонные” боковины.
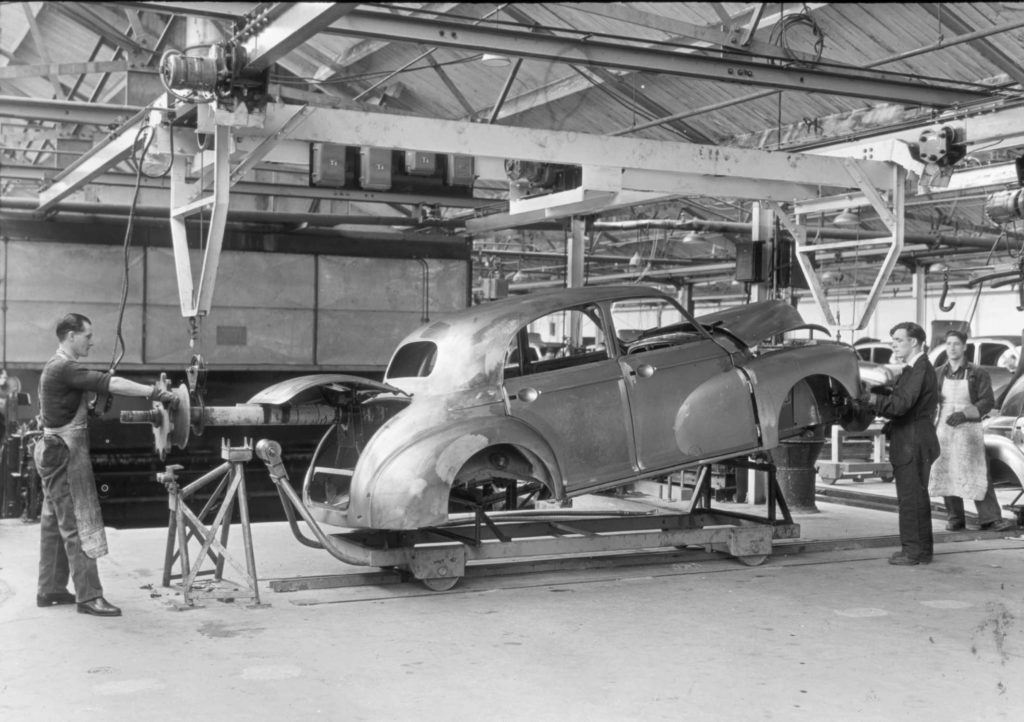
Также припоем могли выполнять и другие работы, в том числе – и исправлять мелкие дефекты, и даже отчасти корректировать зазоры между отдельными панелями (очень часто на фотографиях “голых” кузовов машин тех лет на заводе – и наших, и иномарок – видны полосы нанесённого вдоль торцов дверей припоя). Но основное его количество тратилось именно на пайку швов, и особенно – швов в проёмах дверей, которым по понятиям эстетики тех лет положено было быть по возможности такими же красивыми и гладкими, как и наружной поверхности кузова, во всяком случае – на машине мало-мальски высокого класса. Причём конструкция проёмов отличалась от принятой сегодня, при которой сварка осуществляется за отбортовки, на которые потом надевается резиновый уплотнитель, и из-за этого все швы оказывались на лицевых поверхностях проёма:
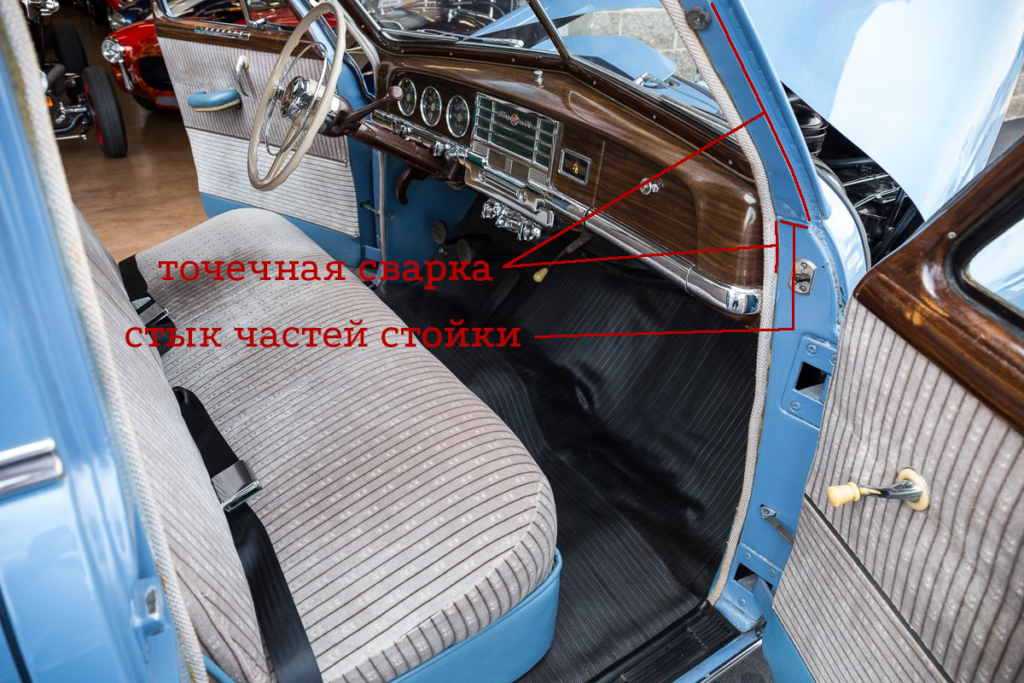
Но об использовании припоя в иностранном автопроме мы ещё поговорим. Что же касается конкретно “Победы”, то в её случае обидный миф появился вследствие невнимательного чтения старой литературы, а скорее всего – одного из отрывков, посвящённого процессу освоения автомобиля в производстве. Шло оно, надо сказать, с исключительным уровнем сложностей, даже с учётом того, что дело происходило в первый год после окончания войны.
Итак, место действия — Горьковский автомобильный завод, время действия — весна 1946 года. На заводе полным ходом идёт подготовка к производству новой модели легкового автомобиля — М-20 «Победа». Это – первый автомобиль, массовое производство которого было подготовлено собственными силами советской промышленности: до этого штамповочное оборудование и пресс-формы кузова заказывались в США, даже на модели, разработанные более-менее самостоятельно. Поэтому задача перед горьковчанами стоит очень сложная и масштабная.
Уже по большей части снята светомаскировка с окон, разобраны оставшиеся с войны руины разрушенных немецкими бомбардировками зданий и сооружений, из цехов вывезен мусор… а в инструментально-штамповом отделе завода (ИШО) без остановки работают «келлеры» — копировально-фрезерные станки — которые переносят сложные пространственные формы будущих панелей автомобиля с изготовленных вручную деревянных моделей на поверхность будущих матриц и пуансонов пресс-форм. Пресс-форм нужно много, очень много: только за май по плану ИШО ГАЗ должен был сдать 35 особо крупных штампов, включая самые главные — те, на которых будут отштамповать пол кузова, крышу и части сварной боковины. В общей сложности в производстве автомобиля должно было быть задействовано около 200 крупных, примерно 600 средних и несколько тысяч мелких пресс-форм, штампов и штампиков. Чтобы высвободить оборудование под изготовление всей этой оснастки для “Победы”, пришлось даже временно пожертвовать цельнометаллической кабиной для грузовика ГАЗ-51 – первые годы его выпускали с деревянной кабиной, обшитой листовой жестью.
Примерно с мая ИШО начинает сдавать первые элементы оснастки для производства кузова, включая самый сложный и трудоёмкий в изготовлении — крупногабаритный вытяжной штамп крыши, состоящий из матрицы, пуансона, прижимного кольца и каких-то там «ещё 85 различных деталей». Окончательно обработка матрицы завершается к 20 мая, а к концу 20-х чисел того же месяца окончена работа и над ответным пуансоном. Это, впрочем, совсем не значит, что только что изготовленный штамп тут же сам собой заработал и начал выдавать детали годного в работу качества – на его отладку ушло ещё немало времени.
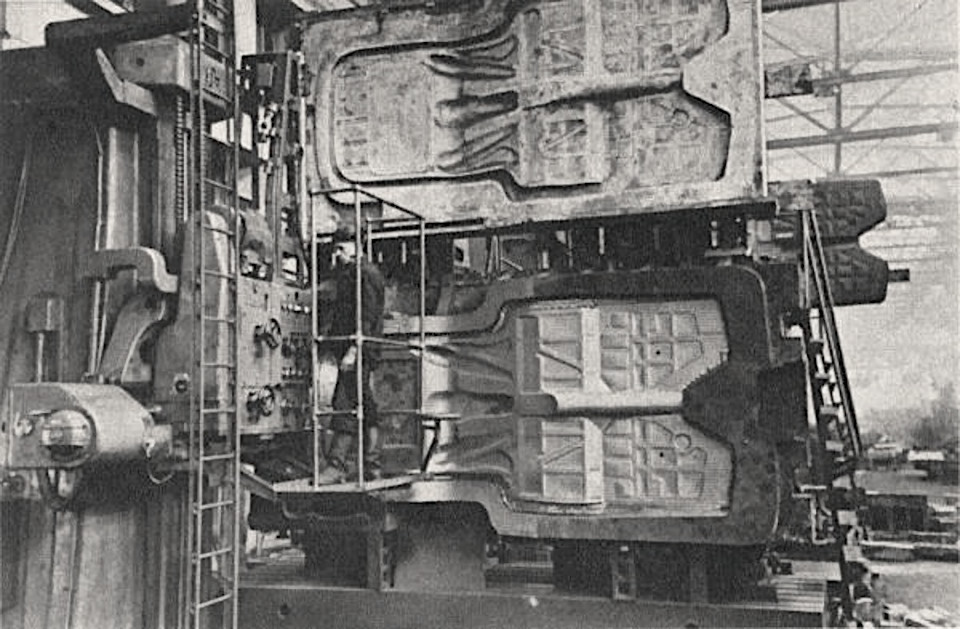
Хуже обстояли дела со штампами для пола кузова и сопутствующих деталей. Не дождавшись очереди на «келлеры», некоторые элементы пресс-формы для изготовления поперечины пола передка делают вручную на обычном вертикальном фрезерном станке.
К сожалению, в целом работа над оснасткой для кузова идёт с огромными проблемами и отставанием от графика. Из 35 крупных штампов за май штамповое производство сдало лишь 13, да и из этих два были приняты «условно», а по факту доделывались уже в июне. Исключительно медленно изготавливается и главный кондуктор, в котором осуществлялась финальная сборка и сварка кузова — его изготовление завершают лишь к 10 июня. Разумеется, в таких условиях график подготовки производства оказывается сорван: срок сборки первого кузова сначала передвинули на 10 июня, но и он остался на бумаге — ИШО так и не смог в установленный срок дать первые вытяжки крыши кузова, угловых панелей и панели приборов. К 12 июня работу штампа налаживают, он даёт первые вытяжки крыши. Но на этом эпопея с ним не заканчивается, так как уже в 20-х числах того же месяца его потребовалось демонтировать с пресса и возвращать в штамповый цех №2 на доделку. И таких моментов при освоении автомобиля, увы, будет ещё очень много.
Только к 21 июня в кузовном цехе №1 была осуществлена сборка и сварка первого кузова «Победы», который затем передали в сборочный цех для дальнейших технологических операций — установки навесных деталей, окраски, шлифовки и обойки (установки потолка и обивок). Правда, для того, чтобы этого добиться, кузовщики, так и не дождавшиеся штамповок крыши, панели передка, переднего кожуха пола, задней колёсной арки и многих других частей кузовных, были вынуждены эти сложные детали раскраивать и выколачивать вручную по деревянным мастер-моделям. Даже по состоянию на конец августа имелось не более 50% от положенного количества производственной оснастки — а выпускать автомобили уже было нужно. Никуда, впрочем, не годились и многие штамповки, сходившие со всё ещё находящихся в стадии наладки штампов — панели пола и крыши, поперечины пола, лонжероны и другие детали приходилось дорабатывать вручную, так как в своём исходном виде они никак не желали влезать в кондуктор.
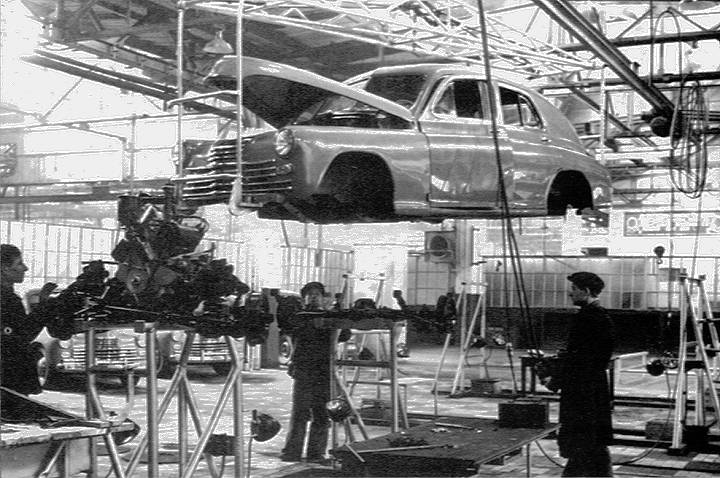
Второй кузов поступил в сборочный цех 1 июля. Впрочем, на этом сборка автомобилей застопорилась — даже в середине месяца оба находившихся в работе автомобиля пребывали в том или ином состоянии неготовности из-за задержек с поставкой комплектующих. К 16 июля в кузовном цехе №1 был изготовлен серийный кузов №5 и начала сварка кузова №6, который был передан в сборочный цех к 25 июля, в цех сборки легковых машин — к десятым числам августа, а на готовый автомобиль стал похож лишь в середине того же месяца. Впрочем, судьба шестого кузова была нелёгкой с самого начала – проблемы вызвал даже процесс переноса его из кузовного цеха в расположенный на втором этаже того же здания сборочный, потому что впервые кузов был сдан с установленным оперением и облицовкой передка, из-за чего не влезал в рассчитанный на более короткие кузова “Эмок” шахтный подъёмник.
Вот про этот самый шестой кузов и были написаны слова, скорее всего ставшие основой для мифа о “семидесяти килограммах олова”. После приключений с подъёмом на второй этаж он попал в руки рихтовщиков и паяльщиков, и со слов авторов посвящённой этому “знаменательному событию” сатирической (!) заметки «Приключения шестого кузова» из вышедшего 26 июля 1946 года №70 заводской газеты-малотиражки, выпускавшейся для работников автозавода работавшей на нём выездной редакцией газеты «Правда»…
…похожи они не на паяльщиков, а на штукатуров. У каждого в руках деревянная лопаточка и паяльная лампа. Все кругом шипит, воет, шумит. Олово льётся рекой.
– А вы думали тяп-ляп и готово, – сказал, посмотрев на наши удивлённые лица, начальних техсектора цеха тов. Греков. – Нет, залатать все неровности на подшефном вам кузове – дело не шуточное. Чтобы привести его в божеский вид, нам придется на него израсходовать семьдесят килограммов олова.
(ссылка на конкретную страницу с этой заметкой)
Видите, в чём проблема ? Фраза про «70 килограммов олова» изначально относилась к самым-самым первым, по сути опытным, автомобилям, которые собирались до запуска конвейера для отладки производственного оборудования. И, естественно, были напрочь кривыми и косыми, что и не мудрено: выколотка многих ответственных кузовных панелей осуществлялась вообще вручную, без штампов. После этого — индивидуальная подгонка всех деталей на стадии сборки, ручная рихтовка дефектов геометрии, образовывавшихся на этапе выколотки, штамповки и сварки, ну, и в конечно итоге — «льющееся рекой» при подготовке к окраске олово… Да ещё надо сделать скидку на сатирический жанр самой заметки, упомянутое в которой число может быть банальной гиперболой, преувеличением, цель которого — как следует “лягнуть” бракоделов с участков штамповки и сварки за плохую работу.
Именно так и выглядит штучная сборка первых экземпляров автомобиля из постановочной партии, осуществляемая «по обходной технологии» — то есть, технологии, временно замещающей нормальный производственный процесс, спроектированный для данной модели и впоследствии используемый при её массовом выпуске. Всего до конца 1946 года таким образом смогли собрать только 23 автомобиля. Причём они хоть и значились как товарные, но фактически большая часть из них осталась на заводе для различных испытаний. Да их и нельзя было сдать заказчикам, потому что они были частично некомплектны из-за того, что некоторые некритичные составные части автомобиля ещё не были освоены в производстве. Первый автомобиль вообще несколько раз разбирали и снова собирали для отработки нюансов процедуры.
Мало-мальски крупномасштабное конвейерное производство «Победы» началось только в апреле 1947 года. Да и тогда шло оно «ни шатко, ни валко» — к февралю 1948 смогли собрать лишь тысячу автомобилей, а всего в первой производственной серии 1946-1948 годов было примерно 1700 машин (в среднем не более 100 машин в месяц, т.е. нескольких штук в день). По другой информации, за 1947 год всего была собрана 601 машина, а за 1948 — 4 549, что всё равно очень мало с учётом того, что машина формально находилась в серии уже два с чем-то года.
У этих машин кузова тоже были далеко не высокого качества — хотя и намного лучше, чем у самых первых серийных экземпляров, поскольку постоянно вводилась новая производственная оснастка и шла отладка уже сданной. Однако, конструкция «Победы» всё ещё оставалась сырой, а технология изготовления — не доведённой до ума, не позволяющей выпускать большие количества машин с приемлемым качеством и низкими затратами, что и является определяющим признаком массового конвейерного производства. Из-за обилия подгонок и прочих выполняемых вручную операций фактически каждый кузов получался «индивидуальным» — из-за плохой отработанности технологии многие штамповки жестянщикам всё так же приходилось дорабатывать вручную.
Главной причиной такой ситуации было то, что после войны с запуском в производство нового, современного легкового автомобиля очень сильно заторопились – “на всё про всё” заводу было отведено менее года. В результате “Победа” была запущена в серию без полноценных испытаний прототипов, а наращивание объёмов её выпуска попытались осуществить параллельно с отработкой технологии производства – то есть, по сути, ради исполнения установленных “свыше” сроков на заводе стали выпускать товарные автомобили по технологии, которая в лучшем случае годилась для изготовления опытной серии экспериментальных образцов, одновременно с отработкой производственного процесса.
В общем – подход “запустим в серию как есть, а доработаем уже в ходе производства”, более-менее работавший в годы войны с танками и самоходками, в случае легкового автомобиля потерпел логичный и вполне закономерный (с точки зрения современного наблюдателя) провал. Видимо, кое-кто забыл, что у “легковушки” помимо технических качеств есть ещё и качества потребительские – она должна иметь товарный вид, хорошее визуальное качество исполнения кузова, красивую отделку, быть комфортабельной и приносить минимальное количество проблем при эксплуатации — и на то, чтобы этого добиться в серии, нужно порой намного больше времени, чем для того, чтобы освоить производство того же танка.
Летом 1948 года “наверху” что-то начали подозревать: вместо крупносерийного конвейерного производства нового легкового автомобиля получился какой-то малосерийный цирк с конями с рихтовщиками и паяльщиками. В сентябре по указанию Совета министров СССР конвейер остановили и стали разбираться, какого чёрта происходит, кто в этом виноват и что со всем этим делать. Вновь его запустили только в 1949 году, и к этому времени сходившая с него «Победа» второй производственной серии стала вполне зрелым в конструктивном и технологическом отношении автомобилем, переболевшим всеми «детскими болячками» и готовым к масштабированию своего выпуска до десятков тысяч в год.
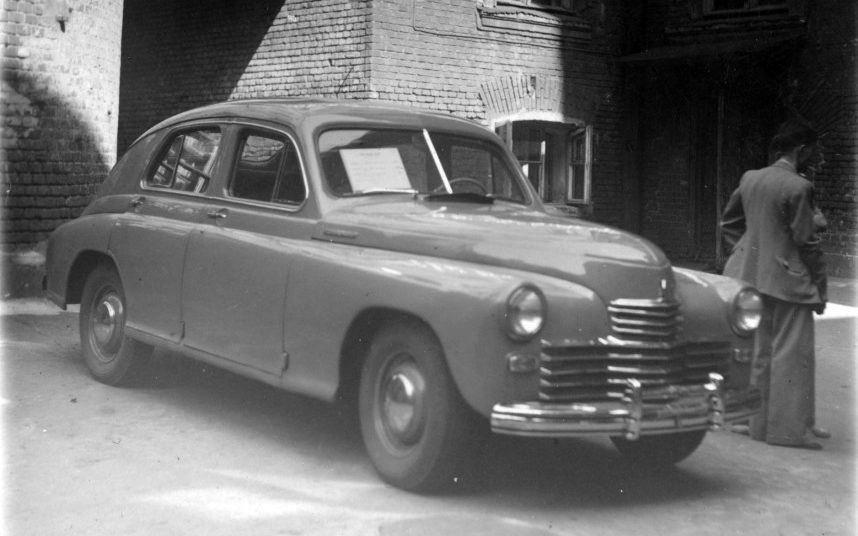
В общем – к серийным автомобилям, которые выпускались массовой серией в 1949-1958 годах, фраза про отвратительную штамповку и десятки килограммов олова имеет очень и очень опосредованное отношение. Они выпускались по совсем другой технологии, с намного меньшей долей ручного труда. Как и положено автомобилям, собираемым на конвейере. Уже сами приведённые здесь цифры масштабов выпуска великолепно показывают абсурдность сравнения вынужденно существовавшей на тот момент обходной технологии изготовления кузовов, с ручной подгонкой, рихтовкой и выравниванием панелей припоем, и использовавшейся впоследствии полноценной, крупносерийной: по обходной технологии автомобиль с кузовом №6 собирали месяц ! А после развёртывания массового производства таких автомобилей каждый день делали уже до сотни штук (и всего до 20…30 тыс. в год).
Заводу намного проще и дешевле один раз доработать пресс-формы, отладить штампы и сварочные кондукторы, чтобы они не гнали брак потоком, чем потом массово его исправлять за счёт малопроизводительного ручного труда.
Хорошим отражением постоянного совершенствования технологии выпуска “Победы” является непрерывное снижение трудоёмкости изготовления каждого её экземпляра, без чего было бы невозможно наращивание темпов выпуска автомобиля. В 1957 году она уже составляла 45% от уровня 1948 года, то есть — её удалось снизить более, чем вдвое по сравнению с наиболее совершенным вариантом технологии, использовавшейся до остановки производства (а если бы её сравнивали с затратами труда на изготовление автомобиля с многострадальным кузовом №6 — то разница составляла бы уже десятки, если не сотни, раз). И в огромной степени это было достигнуто именно за счёт оптимизации процесса изготовления кузова, уменьшения в нём доли ручного труда – включая и пайку.
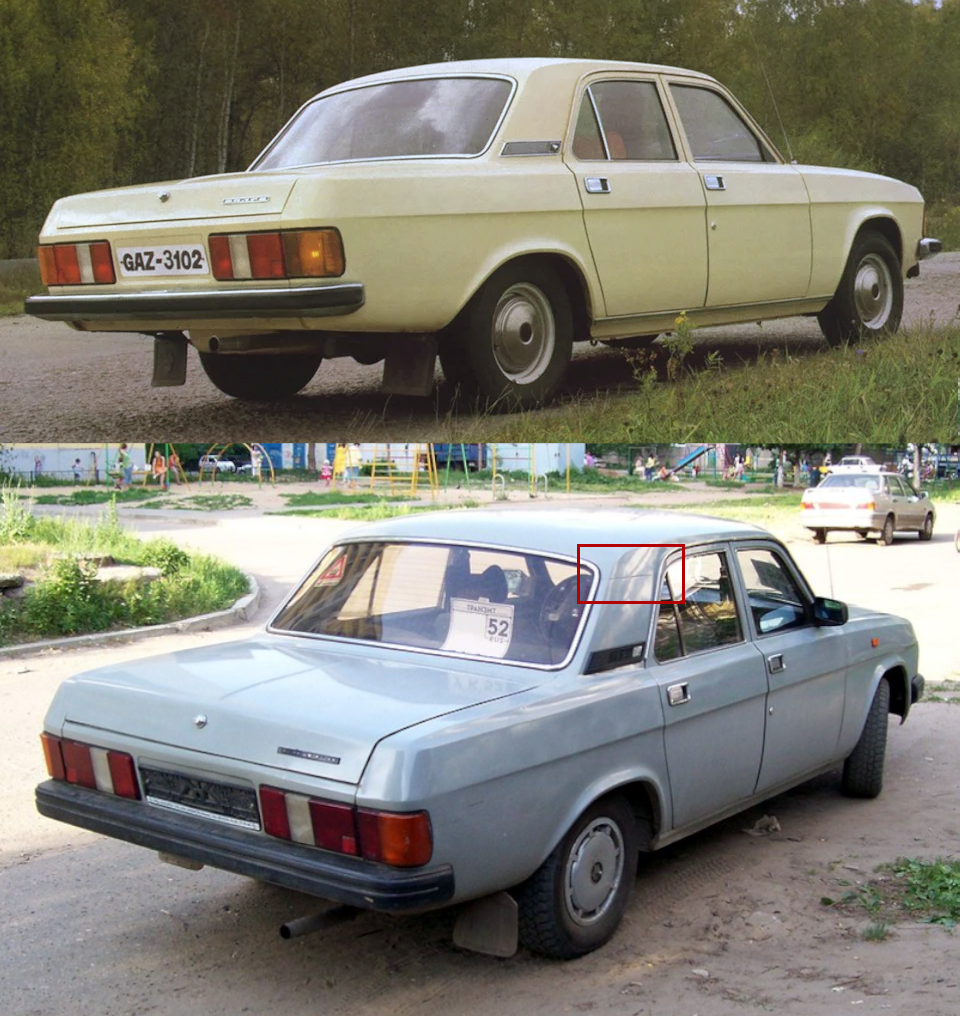
Но полностью пайка припоем как технологический процесс далеко не исчезла. Какое-то количество припоя есть на всех ГАЗовских кузовах, выпущенных до второй четверти шестидесятых годов, да и после этого он использовался при подготовке к окраске части кузовов, в основном — предназначенных на экспорт, с единичными рецидивами вплоть до девяностых годов, если не позже — на ГАЗ-3102 в особых случаях мог облуживаться шов между задней стойкой и крышей, причём чуть ли не до конца выпуска (многие даже думают, что его там нет). Но никак не для того, о чём говорится в мифе, и уж точно далеко не в тех количествах.