Характерной деталью кузова любой “Волги” является шов в месте соединения задней стойки со “скальпом” крыши. Присутствует он абсолютно на всех автомобилях, основанных на 24-ртом кузове, но оформление его может сильно отличаться: где-то он перекрыт накладкой, где-то пропаян оловом и сошлифован до гладкой поверхности, а где-то – изначально выполнен по такой технологии, которая практически исключает необходимость последующей обработки. Но, обо всём по порядку…
На основе публикации: канд. техн. наук И. В. Куликов, В. И. Каманин, А. П. Романчук, О. С. Желтов: “Механизированная дуговая пайкосварка крыш кузовов”, “Автомобильная промышленность”, №5 за 2000 год.
Отштамповать придуманную дизайнерами “Волги” крышу, имевшую достаточно сложную форму, как одну деталь вместе с задними стойками не получалось – в этом случае процент брака при штамповке был бы недопустимо велик из-за превышения допустимого максимального удлинения металла при вытяжке. На ГАЗ-24 и 24-10 панель крыши соединялась со стойкой внахлёст и приваривалась к ней 21 точкой сварки, а затем место соединения для усиления проваривалось полуавтоматической дуговой сваркой в среде углекислого газа прерывистым швом (участками по 15…20 мм). Шов зачищался, рихтовался и для герметизации частично заполнялся пластмассой ТПФ-37, наносившейся методом газопламенного напыления (“чёрная шпаклёвка”, о которой пишут многие владельцы этих машин – на самом деле это не шпаклёвка, а материал, который в начале шестидесятых годов пришёл на смену ранее использовавшемуся для обработки швов припою).
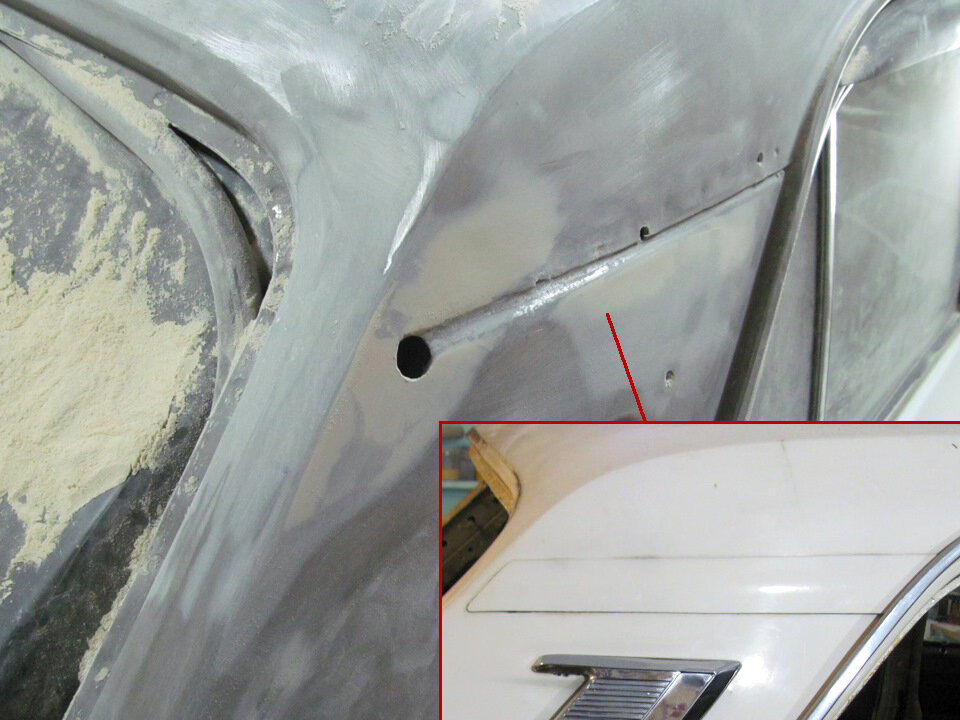
Получалось не очень красиво, но особой роли это не играло – с учётом того, что по технологии это место прикрывалось накладкой, которая полностью закрывала все следы технологии изготовления. Никого не смущали ни периодически случавшиеся деформации кромок панелей, ни даже прожоги металла при сварке. Кстати, абсолютно такие же швы, как правило – заполненные припоем, были в том же самом месте и у американских автомобилей тех же лет, например – у Ford Mustang шестидесятых… восьмидесятых годов. Законы физики по всему миру одинаковы, и то, что на ГАЗе не могли с приемлемым процентом брака отштамповать крышу такой формы целиком, означает что в те годы это наверняка было проблемой и по другую сторону Атлантики:
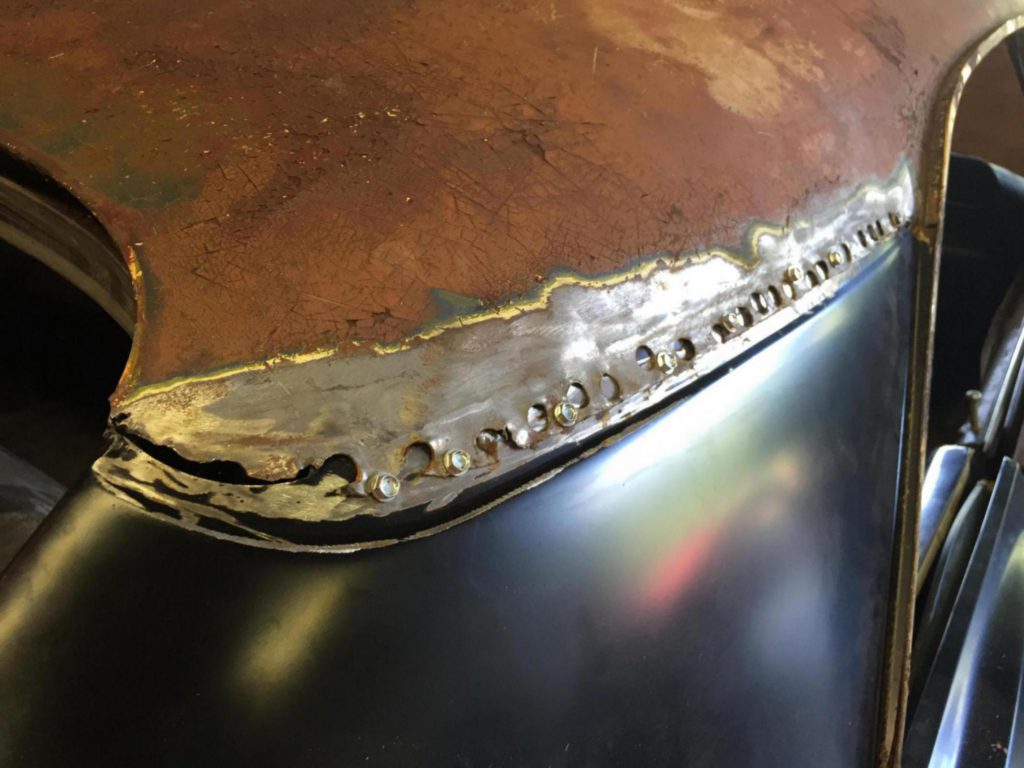
Что касается решения с накладкой, то оно было, конечно, удобно с точки зрения технологии, но ухудшало внешний вид автомобиля и со временем приводило к появлению коррозии из-за скопления под накладкой воды. На ГАЗ-3102 эту часть крыши переработали – шов сделали более аккуратным, а на ранних машинах ещё и заполняли припоем:
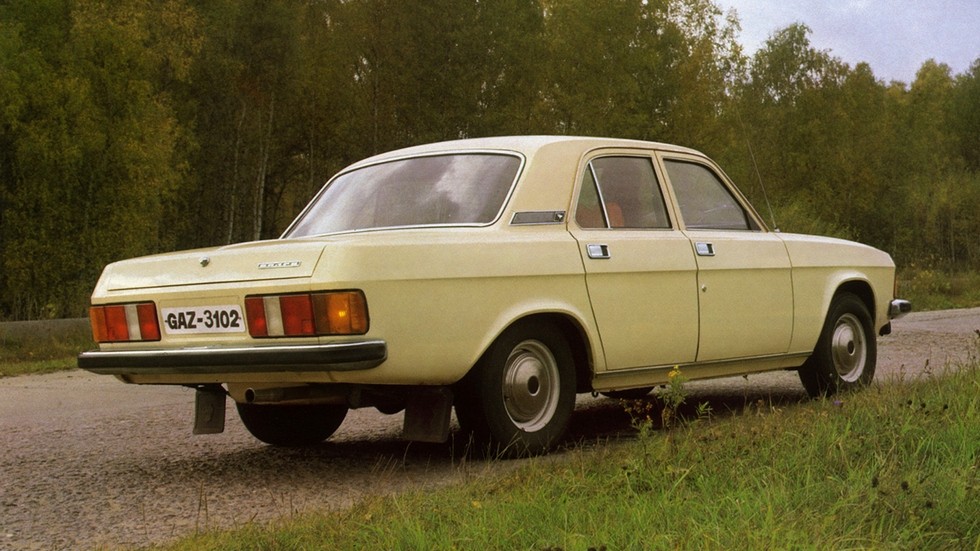
Однако, делать это вручную для массового производства посчитали слишком сложным и дорогим. Поэтому на ГАЗ-31029 и ГАЗ-3102 более поздних выпусков от полной маскировки шва отказались, его просто доводили до более-менее приличного вида:
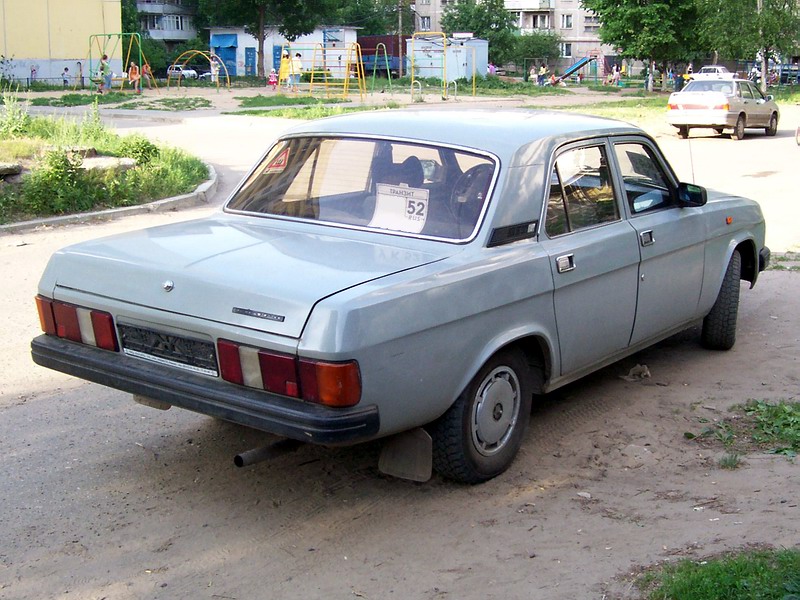
На ГАЗ-3102 (31025) такой подход использовался до самого конца выпуска модели (причём чем дальше – тем меньше старались), хотя на выставочных или собранных по особым заказам машинах этот шов могли и по-старинке полностью убирать припоем.
Между тем, при переходе к ГАЗ-3110 изменили форму крыши “Волги”, сделав её более скруглённой. А шов при этом остался на своём месте. И если раньше он ещё хоть как-то смотрелся в сочетании с чётко отбитым вдоль всей крыши ребром, то теперь уж точно выглядел бы инородным элементом. Первые машины этой модели, выпущенные примерно до конца девяностых годов, шли со швом крыши, выполненным ещё по старой технологии: точечная сварка с усилением прерывистым швом “полуавтоматической”. Требование сделать стойку гладкой привело к тому, что шов приходилось тщательно зачищать “болгаркой” до полного разглаживания, а затем рихтовать и наносить слой шпаклёвки. Однако, такую технологию на заводе считали избыточно трудоёмкой: требовалось принципиально новое решение проблемы, и его нашли.
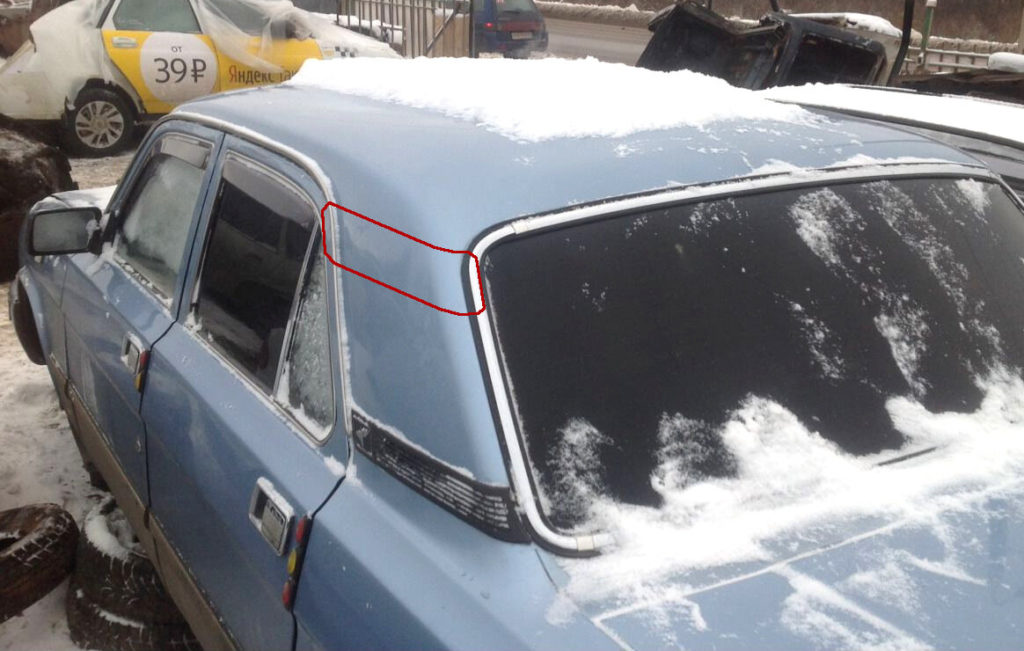
Основным критерием был минимальный нагрев места соединения в процессе обработки, и, соответственно, минимальная деформация выполненных из тонких листов стали кузовных панелей в месте шва. Этому требованию, а также требованиям по технологичности, в полной мере отвечала дуговая пайкосварка тонкой проволокой из цветного металла. При этом процессе кромки соединяемых деталей практически не подвергались нагреву и, соответственно, не деформировались.
Далее идёт прямая цитата из указанной выше статьи, лучше авторов которой я данный технологический процесс не опишу:
Реализовать процесс пайкосварки с таким регулируемым импульсным управлением током удалось, использовав источник питания инверторного типа “Инвертэк STT-11” американской фирмы “Линкольн Электрик”. В состав собранного полуавтомата для механизированной пайкосварки в среде аргона вошли также подающий механизм LN-742 с четырьмя роликами и горелка “Магнум”, обеспечивающие равномерную подачу проволоки малого (0,8—1 мм) диаметра.
В рассматриваемом случае в качестве электродной применили бронзовую проволоку 0,8 Бр А8, разработанную институтом “Цветметобработка” совместно с ОАО “ГАЗ” и обеспечивающую необходимое формирование шва (с плавным переходом к основному металлу), хорошую обрабатываемость абразивным инструментом.
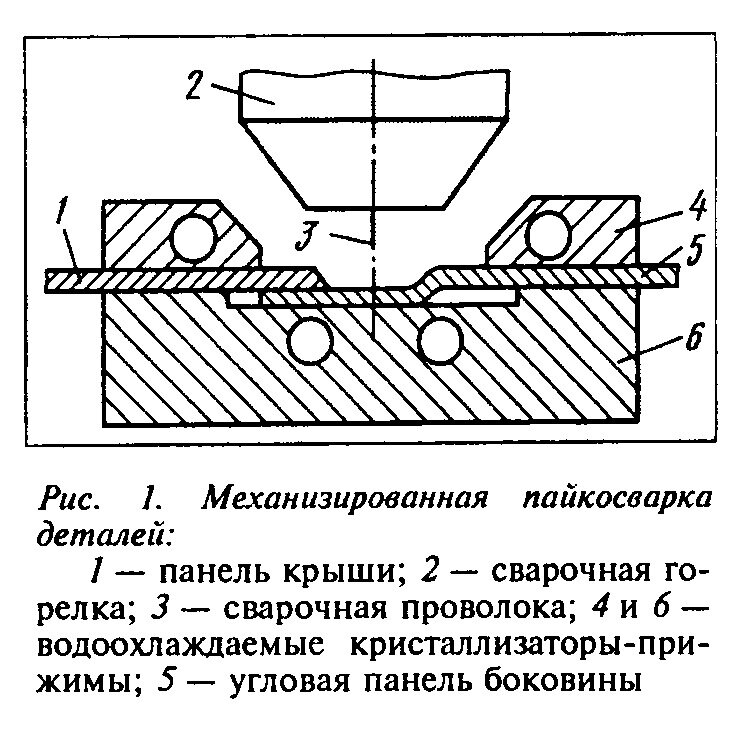
Сборка и последующая механизированная дуговая пайкосварка по новой технологии выполняются в поворотном кондукторе с использованием медных водоохлаждаемых кристаллизаторов-прижимов, дополнительно снижающих деформации металла (рис. 1). В итоге после сварки требуется минимальная зачистка металла шва до уровня основного металла, а рихтовка, герметизация и шпатлевка полностью исключены.
Как показали металлографические исследования, выбранные режимы сварки обеспечивают достаточно плотное соединение деталей и удовлетворительное, с требуемыми геометрическими размерами, формирование шва. При этом соединение образуется за счет диффузионной прослойки с минимальным подплавлением основного металла (рис. 2).
Точная дата перехода на новую технологию в статье не сообщается, но произошло это в самом начале 2000-х годов. Решение оказалось очень удачным – прочность шва была такой, что при испытании на растяжение разрыв происходил не по паяному шву, а по металлу рядом с ним. Успешно выдержали кузова с паяным соединением шва крыши и стендовые испытания, имитирующие циклы нагружения при пробеге в 250 тыс. км. Такая технология успешно использовалась до самого прекращения выпуска модели ГАЗ-31105.
Сама же по себе пайкосварка твёрдыми припоями была довольно широко распространена в автомобилестроении тех лет, а сегодня вытеснена более совершенной технологией – лазерной пайкосваркой, которая применяется, в частности, на продольных швах, идущих вдоль крыши современных автомобилей в месте её соединения с боковинами, или вокруг проёма и на кромке крышки багажника. В этой роли она также пришла на смену пластиковым накладкам, которыми эти швы как правило закрывали на автомобилях прежних поколений.