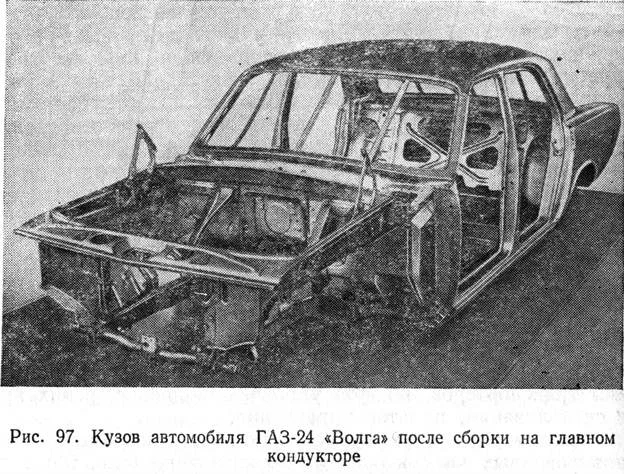
Как и практически все кузова легковых автомобилей по настоящее время, кузов “Волги” ГАЗ-24 сваривался из отштампованных на прессовом оборудовании стальных панелей, которые соединялись в сварочных кондукторах (приспособлениях для фиксации деталей, подвергающихся сварке) при помощи осуществляемой за отбортовки деталей точечной сварки, с эпизодическим использованием ручной электродуговой (электродной) для усиления ответственных швов.
Это в общих чертах – а на практике процесс изготовления кузова этой модели имел немало специфических особенностей.
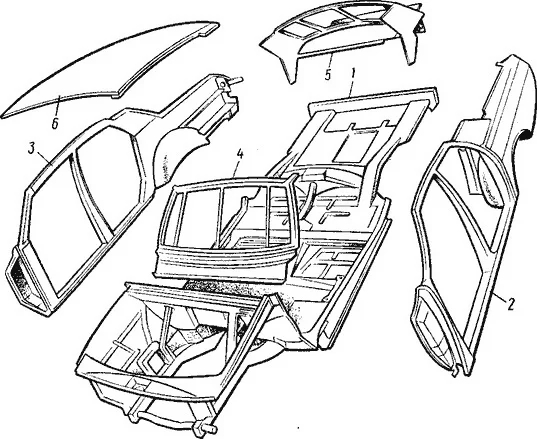
Окончательная сборка кузова ГАЗ-24 осуществлялась из 6 крупных предварительно подсобранных узлов (см. рисунок) — панели пола, левой и правой боковин в сборе с задними крыльями, рамок лобового и заднего стёкол и крыши (без учёта навесных элементов, крепящихся на болтах).
Для сравнения, у «Победы» кузов собирался из 11 узлов, а у «Волги» ГАЗ-21 на заключительном этапе её выпуска — из 7. Кузов автомобиля ВАЗ-2101 «Жигули» также собирался из 6 крупных узлов, то есть, в этом плане разработанная на ГАЗе технология была не менее совершенна, чем фиатовская (правда, у «Жигулей» сюда входили и приварные передние крылья — что имело как плюсы, так и минусы с эксплуатационной точки зрения).
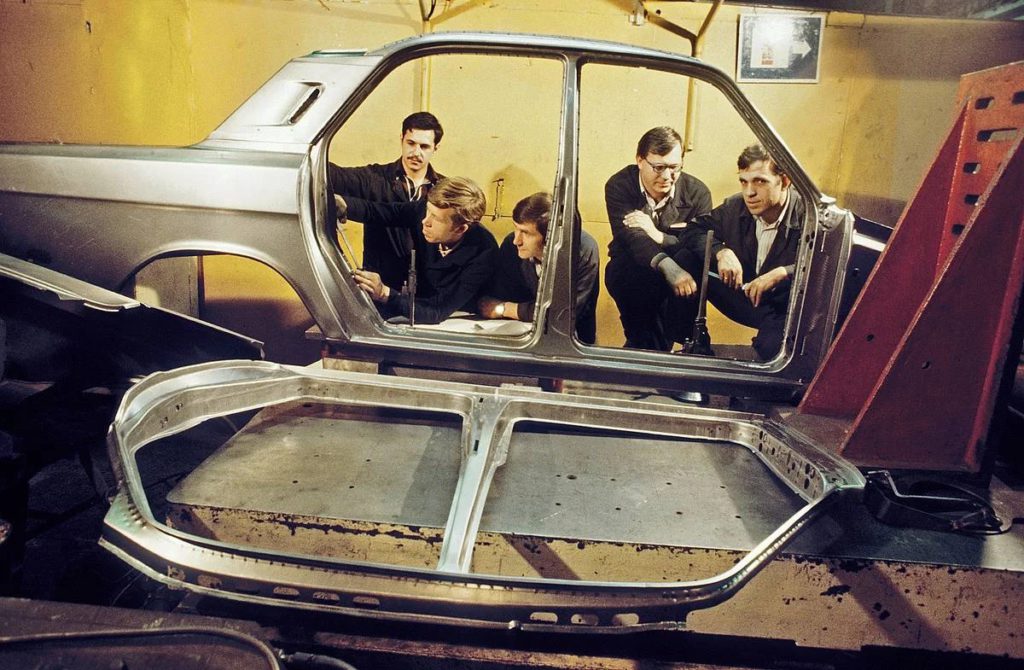
Меньшее число сборочных единиц в данном случае означает меньшее число операций по сопряжению отдельных кузовных панелей при сборке, каждая из которых создаёт возможности для отклонения от заданных размеров. Например, проёмы дверей цельноштампованной боковины кузова всегда имеют строго одинаковую геометрию, так как образующая их штамповка сходит с одного и того же штампа — в отличие от сваренной в кондукторе из пяти отдельных деталей (передней, задней и центральной стоек, порога пола и рейки крыши) боковины «Победы» и ранних выпусков «21-й», у которой геометрия «плавала» в широких пределах. При этом следует помнить, что у «Победы» и «21-й» «телевизор» передка и задние крылья тоже были навесными деталями — то есть, фактически общее число осуществляемых при сборке автомобиля сопряжений было ещё больше.
Собирать кузов из небольшого числа крупных панелей намного быстрее и выгоднее, чем из большого числа мелких, хотя и сложнее в технологическом плане (в частности — для этого нужны особо крупные и мощные штампы, а также листовые заготовки нестандартного размера из особо мягкой, хорошо вытягивающейся при штамповке, стали).
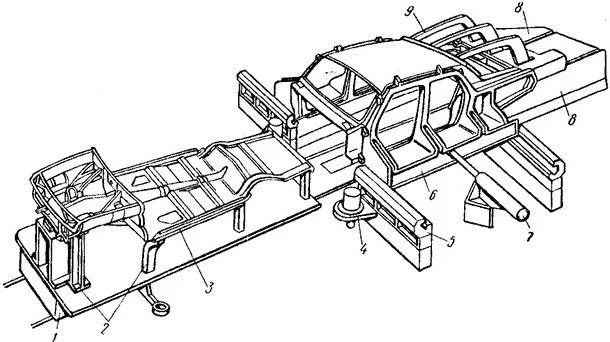
Для сборки и сварки кузова ГАЗ-24 использовалось шесть стационарных кондукторов, включая несколько сравнительно простых, предназначенных для подсборки отдельных узлов — основания кузова, боковин и т.п., и весивший 12 тонн главный кондуктор, служивший для окончательной сборки (см. рисунок выше), работа которого была в значительной степени механизирована за счёт пневматических и гидравлических сервоприводов. Особое внимание было уделено упрощению технологических операций и снижению трудозатрат — в частности, рациональному расположению фиксирующих приспособлений и уменьшению их размера и массы.
Сборка кузова осуществлялась в следующей последовательности. Сначала в фиксирующие устройства кондуктора устанавливались проём заднего окна, боковины кузова и проём переднего окна. В проемах ветрового и заднего окон при этом были установлены технологические усилители, которые обеспечивали жёсткость детали и отсутствие деформации проёма при сборке и сварке кузова. Затем вместе с фиксирующими устройствами их при помощи гидропривода подавали в рабочее положение и приваривали к ним крышу. После этого тележка с закреплённым на ней основанием кузова, включая подмоторную раму, подавалась внутрь кондуктора и приводилась в рабочее положение поднятием на 200 мм за счёт винтового механизма с электроприводом. Сваривая основание кузова с боковинами и проёмами стёкол по выступающим фланцам, получали готовый к дальнейшим технологическим операциям кузов в сборе без навесных деталей.
Общее число точек сварки, выполняемых в главном кондукторе, достигало пяти сотен. Для этого главный кондуктор был снабжён шестью подвесными сварочными машинами с ручными пистолетами. После сварки осуществлялся осмотр проёмов кузова и мест установки агрегатов с контролем соблюдения геометрии.
Такая технология была не самой передовой для того времени и сравнительно малопроизводительной — в час бригада из трёх человек могла собрать не более трёх-четырёх кузовов — что, впрочем, вполне соответствовало масштабам выпуска «Волги». Для сравнения, использовавшийся на ВАЗе «фиатовский» подвижный кондуктор проходного типа с челночной загрузкой позволял сваривать до 100 кузовов за одну смену (если принять длину смены за стандартные 8 часов — получается производительность в 12…13 кузовов в час), при этом многие сварочные швы выполнялись многоэлектродной машиной, которая за один технологический приём ставила сразу 96 сварочных точек — при их общем числе в 278. На АЗЛК, реконструкцию которого производила фирма Renault, сборка и сварка кузовов осуществлялись на передовой для того времени механизированной поточной линии производительностью 52 кузова в час.
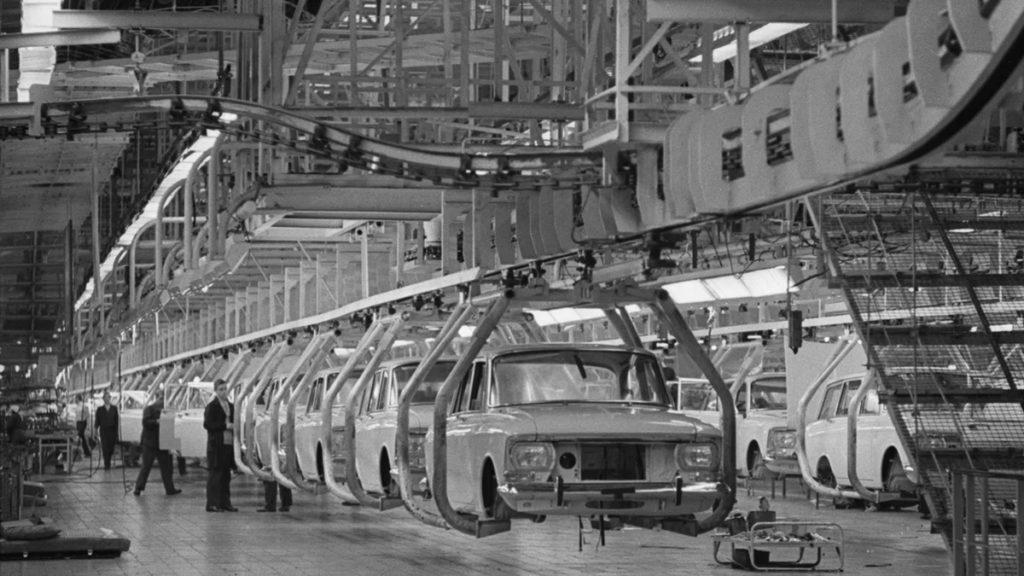
Однако, эти заводы по объёму выпуска легковых автомобилей превосходили ГАЗ во много раз (например, ВАЗ имел примерно в десять раз большую проектную мощность легкового конвейера), так что сравнивать их технологические процессы напрямую некорректно — они изначально создавались под совершенно различные масштабы производства.
Кстати, это — одна из составляющих ответа на вопрос о том, можно ли было увеличить выпуск «Волги» в два / три / несколько раз ? В теории — можно, но на практике для этого фактически потребовалось бы создать для неё «с нуля» полностью новую технологию производства, адаптированную для таких масштабов выпуска — как это было сделано с «Москвичём» 408/412 в ходе реконструкции завода при участии французов, когда выпуск с порядка 50 тыс. машин в год резко возрос до 200 тыс. Для этого по сути понадобилось возвести рядом со старым новый завод с новыми сборочными линиями. Ту же пропускную способность главного сварочного кондуктора без переделки всего техпроцесса штамповки, сборки и сварки кузовов по образцу тех же ВАЗа или АЗЛК увеличить не получилось бы. И такие проблемы возникали бы при попытке серьёзного масштабирования объёмов выпуска не только на каждом этапе производства на самом ГАЗе, но и на каждом предприятии-смежнике.
На практике даже в середине девяностых, работая с полным напряжением всех сил в три смены по 6 дней в неделю, с тотальным проседанием качества за счёт максимально возможной экономии материалов и упрощения всех технологических процессов, ГАЗ сумел нарастить выпуск «Волги» лишь с 65 до 124 тысяч автомобилей в год — т.е. даже близко не приблизился к проектным 500-600 тыс. автомобилей в год АвтоВАЗа. При том, что спрос на продукцию завода намного превышал предложение.
Единственными способами превысить названную выше цифру годового выпуска были бы: либо построить рядом второй такой же завод, который давал бы дополнительные ~120 тыс. автомобилей в год (при сохранении старой технологии), либо полностью реконструировать уже имеющийся под новую, намного более эффективную, технологию производства, и за счёт этого выпускать на тех же площадях больше машин. Оба варианта потребовали бы широкого привлечения зарубежных партнёров и такого масштаба вложений, на который у отрасли не было денег ни до, ни, тем более, после развала СССР, во всяком случае — вне привязки к освоению на заводе принципиально новой модели, с которой всё это имело бы смысл.
С участка сварки кузов шёл в подготовку к окраске. На этом этапе производились зачистка точек сварки, рихтовка, герметизация некоторых швов кузова при помощи газопламенного напыления порошка тёмно-серой пластмассы ТПФ-37 (предшественника современного синтетического шовного герметика) и шлифовка поверхности.
Отрихтованный кузов поступал на участок фосфатирования (бондеризации). При этом химическом процессе на поверхности металла образовывался слой нерастворимых в воде фосфорнокислых соединений, который сам по себе не являлся защитным покрытием, но значительно улучшал сцепление с металлом последующих слоёв грунтовки и эмали. Фосфатирование осуществлялось на специальном агрегате, состоявшем из шести огромных ванн, в которые кузов можно было погрузить целиком. Первая ванна содержала раствор едкого натра, в ней осуществлялось обезжиривание поверхности металла. В последующих ваннах осуществлялись промывка кузова и собственно фосфатирование в разогретом растворе соли фосфорной кислоты – монофосфата цинка – с добавлением селитры и углекислой меди. Так как процесс шёл с использованием агрессивных химикатов, установка была полностью закрыта, а фосфатирование происходило практически полностью в автоматическом режиме: кузов исчезал с глаз на входе в агрегат, а наружу появлялся уже покрытым слоем фосфата и высушенным.
Сразу же после фосфатирования осуществлялось грунтование кузова методом анодного электроосаждения (анафореза). Для этого кузов помещался в ванну с водной эмульсией грунта и подводился электрический ток, таким образом, что сам кузов становится положительным электродом, а дно ванны – отрицательным. Под действием постоянного тока получившие отрицательный заряд частицы грунта начинали перемещаться к положительному полюсу – кузову – и равномерно оседали на его поверхности, причём процесс шёл только до достижения покрытием определённой толщины, так как после этого слой грунта начинал служить в качестве изолятора и осаждение в этом месте прекращалось.
Сегодня анодная технология считается устаревшей – её вытеснило катодное электроосаждение грунта (катафорез). Но по тем временам это был большой прогресс по сравнению с грунтованием обычным погружением в ванну – не говоря уже о нанесении грунтовки ручным распылением, как это делалось до середины пятидесятых годов. В результате анафорезного грунтования вся поверхность кузова, включая выступающие рёбра, внутренние полости и даже щели сварных швов, покрывалась равномерным по толщине слоем грунта. Дополнительным плюсом электроосаждения, очень важным в заводских условиях, была пожарная безопасность, что что достигалось благодаря использованию в этом процессе водной эмульсии, а не грунта, разбавленного горючим растворителем, как при грунтовании погружением.
После горячей сушки загрунтованный кузов шлифовался «на мокрую» водостойкой шкуркой, промывался тёплой водой и поступал по конвейеру в камеру нанесения жёлтого глифталевого грунта-шпаклёвки, который заполнял мельчайшие неровности на поверхности кузовных панелей. Сушка грунта осуществлялась при температуре 130—140°С. Затем на кузов наносился слой финишной грунтовки, который также подвергался горячей сушке и очень тщательно шлифовался, при необходимости – с ручной шпаклёвкой отдельных мест. После этого кузов считался готовым к окрашиванию.
Окраска производилась синтетической меламин-алкидной эмалью в два слоя («проявочный» и основной) с горячей сушкой и промежуточной шлифовкой. Общая толщина покрытия составляла до 100 микрон, а при считавшейся допустимой в случае образования незначительных дефектов локальной полной перекраски – до 120 микрон.
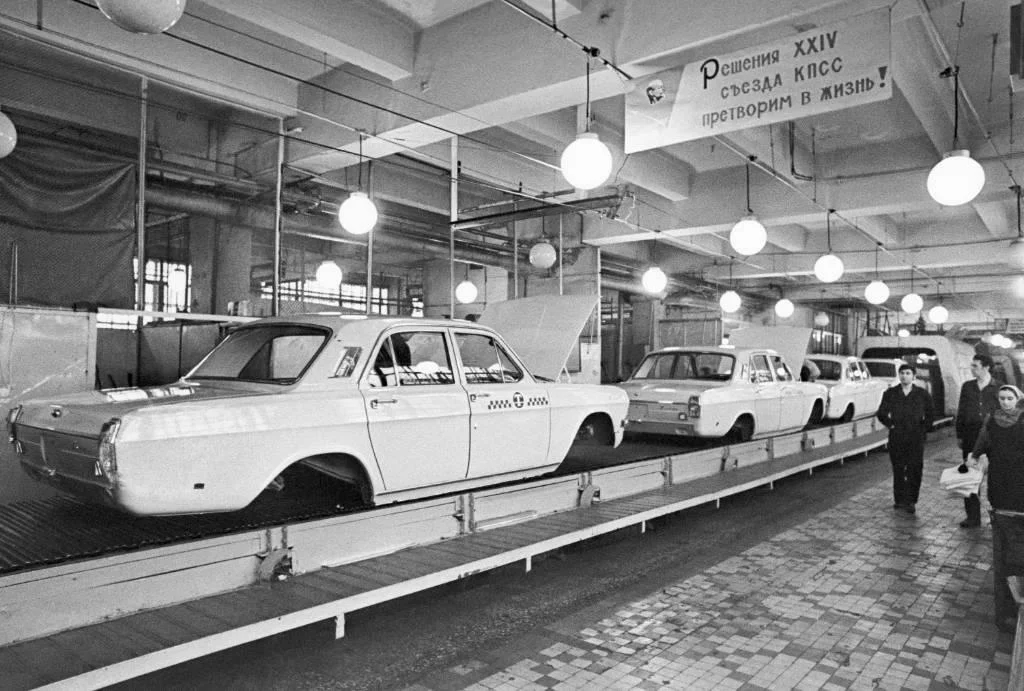
Цвет, в который окрашивался кузов, зависел от времени его выпуска – расцветки эмали ротировались раз в неделю в соответствии с утвержденным графиком. В первую очередь старались окрасить чёрные кузова, поскольку они требовали особой чистоты оборудования и отсутствия запылённости на участке, чего можно было достичь только сразу после профилактики окрасочной линии. Причём под окраску в чёрный цвет часто шли лучшие из кузовов, потому что на чёрном цвете хорошо видны все недоработки, допущенные при подготовке к окраске. Из-за использования данной системы как правило получалось так, что автомобили каждой партии были одного и того же цвета. Иногда это было плюсом, например – для поставок автомобилей в такси.
После окраски на поверхность днища и колёсных арок наносилась мастика №579 (либо №213, №580, БПМ-1) – вручную или пневматическим распылением. Изнутри на пол производилась наклейка матов листовой вибродемпфирующей мастики. Наружные панели дверей и переднего щита шумоизолировались вафельным картоном, а крыша – вспененным полиуретаном (поролоном). Багажник изнутри ещё до окрашивания кузова покрывался мастикой.
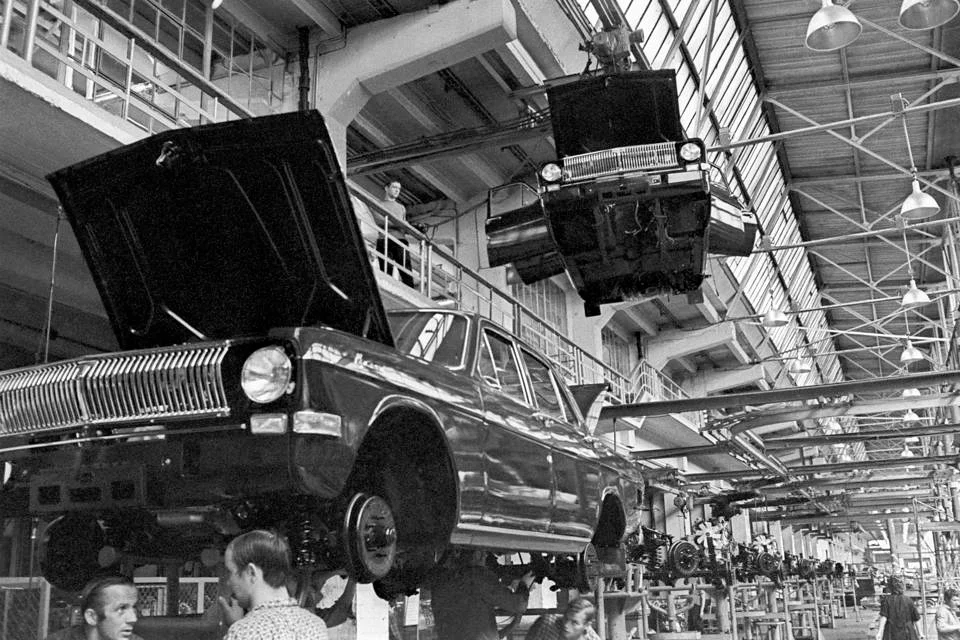
В готовый кузов вставлялись стёкла с уплотнителями, устанавливались фурнитура, детали отделки, обивка и прочие элементы салона, осветительные приборы. В таком виде собранный кузов «первой комплектации» отправлялся либо на сборочную линию, либо в запчасти.
С середины 1980-х годов внутренние полости кузова обрабатывались на заводе антикоррозионными препаратами группы МЛ-2 — НГМ-МЛ, Мольвин, Мольвин-МЛ.